As mountain bikers, we love to obsess over our bikes. For some it could be a fixation on suspension performance while others may count the grams to make their XC rig as light as possible.
Helmets however are often taken for granted—until you really need it in a crash that is. While buying a new helmet mightn’t seem as exciting as purchasing some carbon trinket, a lot of technology and testing goes into the creation of each and every helmet. Giovanni Caporali and Eric Cendral from Limar know all about the behind the scenes side of helmet development.
Limar was one of the first brands to employ expanded polystyrene (EPS) in bicycle helmets. Giovanni is their managing director and has been involved in helmet design and manufacture since 1988. While they are an Italian brand, they sell globally covering everything from kids’ helmets to pro-team roadie lids and MTB helmets.
According to Giovanni, they’ve always had the goal of being the lightest while also being well ventilated and compact. “Of course the overriding aim for any helmet is to protect your head. In order to have the best helmets possible, we decided from the outset – over 20 years ago – to design every helmet to pass all international standards.”
Making helmets light but also safe is no small task. Currently there are three main standards for bicycle helmets; CE in Europe, CPSC for North America and the AS/NZS 2063 standard for Australia and New Zealand. Many brands are made to pass US and European standards, then modify them to meet the specific requirements of Australian testing. Limar designs from the ground up with all of the standards in mind.
With our geographical isolation and comparatively small population, Australia often falls off the radar when it comes to the latest cycling developments. But as far as bicycle helmets go, we are actually in a fairly unique position. Australia and New Zealand are the only nations where helmets are mandatory for riding a pushbike. While cycling doesn’t enjoy the same level of mainstream popularity as in Europe, the fact that we all have to wear helmets makes us one of the larger markets globally, and one that manufacturers pay attention to.
Testing-Testing
While the potential for sales is attractive, our unique certification system doesn’t make it easy. According to Giovanni, “Before you can certify the actual product, the quality systems employed in the production line need to be certified by a third party.”
Next up the actual helmet needs to be tested by an independent laboratory. The series of tests includes dropping the helmet onto a flat anvil with a head form inside—this tests the ability to absorb an impact. Then there’s a localised load distribution test that simulates an impact on an angled object such as a protruding rock. The AS/NZS 2063 standard also looks at the retention system, a test that ensures the straps can’t stretch too much. Interestingly, all these tests are conducted on the one sample. A single helmet needs to hold together through each of these steps; an element that’s unique to the AS/NZS 2063 standard.
Another hurdle for manufacturers looking to capitalise on the Aussie market is the batch testing. After the design gains its initial approved, ongoing checks are required. “To begin with, four helmets from every 500 are destroyed to check that the production has the same characteristics of the original sample,” Giovanni explained. “Once the test is okay you can release the product and deliver them to the distributor. After you have consecutively passed 10 batch tests without any problems, you can then drop down to four helmets in every 1,000 produced.” Limar has 37 different AS/NZS 2063 approved models in their line-up—that’s a lot of helmet testing!
The helmet manufacturer has to foot the bill for all these tests and Eric Cendral estimates that it may add around $1 to the cost of each helmet. However it would cost a lot more if a helmet failed when presented for testing—exponentially so if tooling changes were need at the factory to fix a particular weakness. To combat this, Limar has set up their own in-house testing facility, another expense but one that allows them to be quite certain that a helmet will pass when presented for the third party testing.
So does this strict test regime lead to safer helmets? “Yes of course,” says Eric, “CE is a good standard while CPSC is a more difficult one in terms of shock absorption. Australian testing is the most demanding overall. The straps need to be very strong and the load distribution test can be applied at any point during the test procedure. It means you must build a really good helmet to pass the AS/NZS 2063 standard. This combined with the ongoing batch testing guarantees the consumer a good product.”
Moving to MIPS
While the AS/NZS 2063 standard is clearly seen as a positive safety measure, we asked whether they felt the Swedish designed MIPS system offered any real benefit. At the time Limar didn’t have any MIPS equipped helmets in their line but Giovanni said they are soon to be released. “I think it’s a good system and you will see it on our Ultralight Plus model at the Taipei Show. This will be the lightest MIPS equipped helmet on the market.”
The MIPS system allows a degree of low-friction ‘slip’ between the helmet and your head that aims to reduce the rotational forces when you hit something at a shallow angle—it’s said to lessen the chance of brain injury. Limar plans to introduce MIPS as an option on their top-end road helmet and filter it through their range from there. “MIPS in Sweden charges a licencing fee to use their technology and it’s easier to absorb this cost within the higher-end helmet models,” Eric explained.
Helmet Longevity
As you can see, there’s a fair bit that goes into producing a safe helmet and this means a good helmet won’t be all that cheap. So having made this investment, how long will your helmet last? We asked Giovanni; “Technically speaking EPS and polycarbonate have a very long life. They keep their characteristics for many years and more than 90% of the characteristics are long lasting.
“Technology is always improving and current model helmets are much better than the ones from five years ago, so even if you haven’t crashed or damaged the helmet, there’s some advantage in updating every few years. My recommendation is to change helmets as you’d change your jersey or tyres. You probably wouldn’t want to ride with five-year-old tyres – they could be perished and dangerous – so apply the same philosophy to your helmet.
Caring for your helmet will extend its usable life. Eric explained, “Store it in a cool, dry place, never leave it in the hot sun and don’t drop or bash it around. Of course it’s really important to replace a helmet if you’ve hit your head in a crash. After an impact the EPS will not have the same characteristics and mightn’t protect you if you crash again. We have this crash replacement program that is if you crash wearing a Limar helmet we will replace the helmet at close to half price.”
So aside from the introduction of MIPS, what does Giovanni foresee in the future for Limar helmets? The main theme seems to be diversification; “Currently we have special helmets for downhill and different designs for enduro, there are lightweight helmets for cross-country and special helmets for women. There are so many different riding styles each with differing demands. Our range needs to diversify and keep pace with this—we need to deliver the features and style that people want whilst still sticking to our core goal of producing lightweight and super safe helmets.”
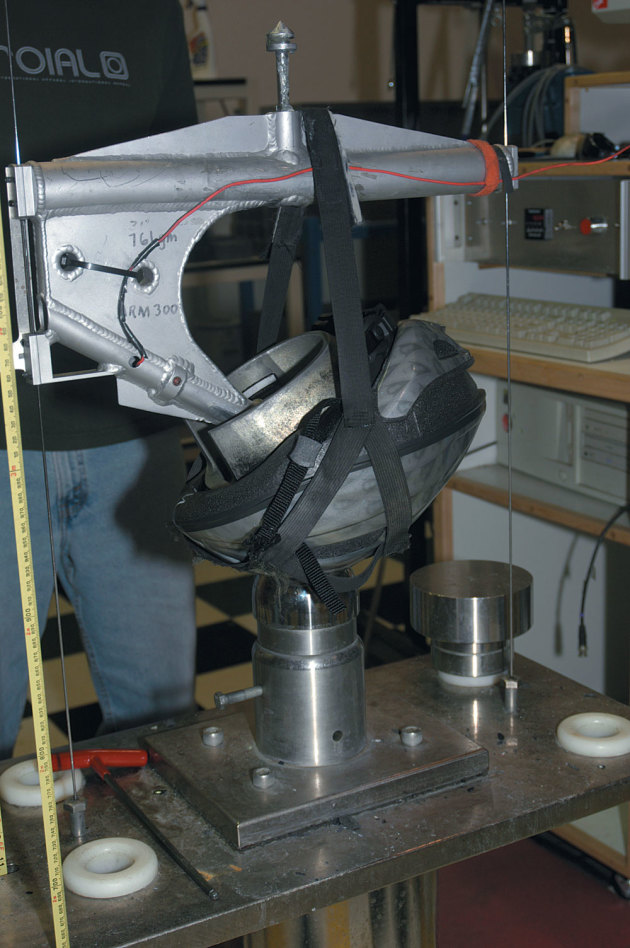
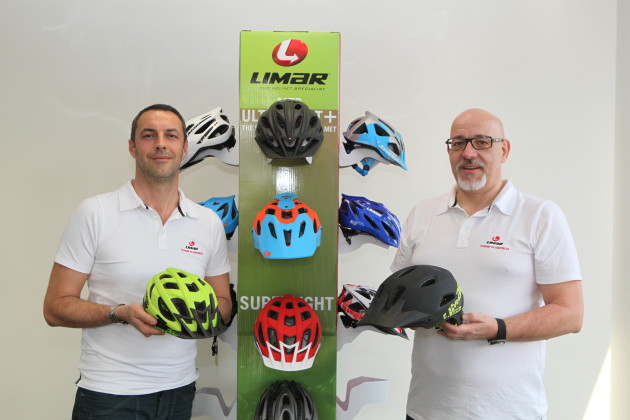